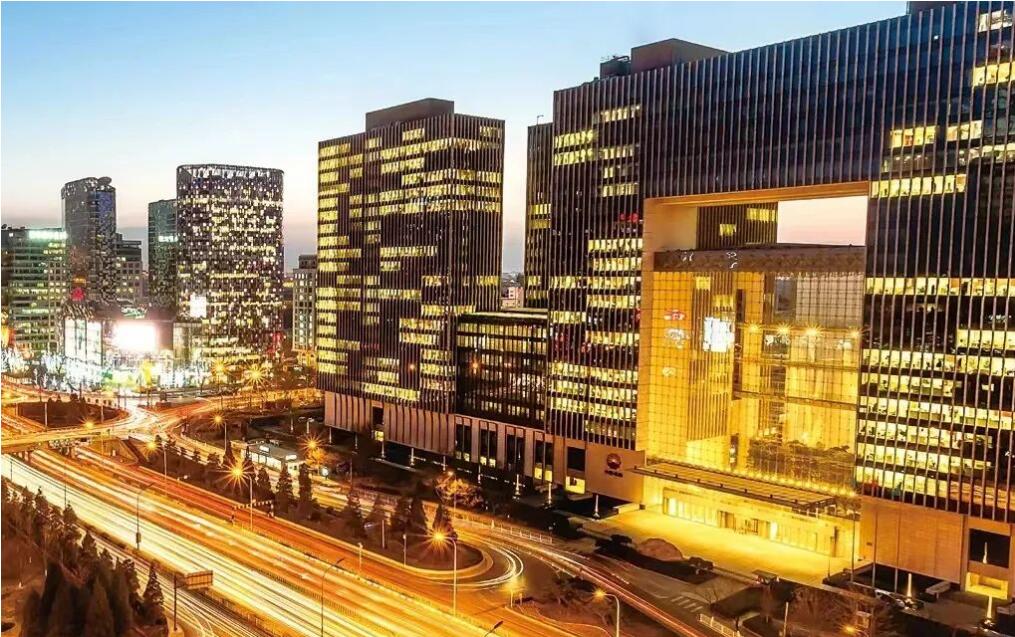
The pipeline is the main means of transportation of the production device, the supply of its materials, the flow of the process are to rely on different specifications, different pressure levels and shapes of the pipeline to achieve, in the extended curved pipeline, there are countless flanges, elbows, welds and other interfaces, if there is a welding failure or out of control leakage, will seriously threaten the normal operation of the device. If it is toxic, harmful, flammable, explosive, corrosive media, such as leakage, easy to occur poisoning, fire, explosion and other casualties, serious pollution of the surrounding environment damage people’s health. How to use pressure plugging (528) technology has become a more important technology in production when there is no need to stop the device for processing. Plugging with pressure is a new advanced equipment maintenance technology. When a part of the equipment pipeline, valve, flange in the production unit leaks, it can quickly block the leak with pressure and temperature without stopping and without affecting the production, so as to ensure the stability of production, make the equipment system run for a long period, and improve economic benefits. The application range of pressure plugging is vacuum to 32MPa and temperature is -20-650℃. Because of its strong applicability, easy operation and good effect, it has developed rapidly in recent years, and is widely used in industries and departments of various processes such as petroleum, chemical industry, electric power, metallurgy and medicine.
Forms and factors of pipeline leakage
1, straight pipe leakage
The leakage failure of the straight pipeline may be caused by the manufacturing defects of the pipeline itself and the quality problems of the pipeline fittings, or it may be caused by the corrosion caused by the welding of the pipeline, the pairing of the pipeline or the inappropriate selection of the pipeline material.
- Elbow leakage
Elbow leakage is mostly on the large radius outside the elbow, when the medium flows through the elbow, it is subjected to the resistance of the elbow, and the medium erodes the elbow leading to leakage failure. In addition, the improper selection of the material of the elbow results in poor corrosion resistance of the material and unreasonable connection structure between the elbow and the straight pipe, leaving a gap that can cause the corrosion medium to remain and concentrate. Accelerated corrosion is an important cause of elbow leakage failure.
3, pipe flange leakage
The sealing of the pipe flange mainly relies on the pre-tightening force of the connecting bolt and achieves sufficient specific sealing pressure through the gasket to prevent the leakage of the sealed pressure fluid medium. There are many reasons for its leakage, the sealing gasket compression force is insufficient, the roughness of the joint surface does not meet the requirements, the deformation of the gasket and the mechanical vibration will cause the sealing gasket and the flange joint surface to leak. In addition, the deformation or elongation of the bolt, the aging of the gasket, the reduction of the resilience, and the cracking will also cause the flange surface to be loosely sealed and leak. Flange leakage also can not be ignored human factors, such as the sealing gasket installation bias, so that the local sealing pressure is insufficient and the tightening force is excessive, exceeding the design limit of the sealing gasket, and the flange fastening process uneven force or the center line of the two flanges offset, resulting in false tightness phenomenon are prone to leakage.
Principle and advantages of plugging with pressure - Technical principle of plugging with pressure
When medium leakage occurs during operation of the device, a sealing cavity shall be established by bandaging, isolating or making fixture to contain the leak point without changing the working conditions or affecting the operation of the device. By injecting sealant (528) into the sealing cavity, the coordination between the advancing speed and the curing time of the sealing injection shall be controlled according to the system temperature and the rheological characteristics of the injection to ensure the filling effect of the injection. The sealing layer injected into the sealing cavity is uniform and dense, and an effective sealing specific pressure is formed, and the leakage is prevented, thus establishing a new sealing structure.
2, with the advantages of pressure plugging
(1) The system does not need to stop, thus ensuring the long cycle operation of the device.
(2) It is not necessary to perform pressure relief replacement on the system.
(3) Avoid the loss caused by the shutdown of the device and damage to other equipment.
(4) greatly reduce economic losses and environmental pollution.
Related technology introduction
According to the specific conditions of the production site, general leakage can be eliminated by replacing the pipe, replacing the flange gasket or welding the hole in the case that the process medium can be temporarily isolated and handed over. However, for the pipeline in the key part of the device, the working condition is flammable and explosive media can not be isolated or can not be welding fire operation, then the corresponding pressure plugging technical means must be taken to eliminate the leak to ensure the safe and stable operation of the device.
1, pipeline leakage with pressure plugging technology
1.1 Rapid strapping and plugging technology
The rapid bundling and plugging technology is applicable to straight pipes, elbows, reducing pipes, pipe hoops, and flange roots with specifications ≤DN300mm, and is applicable to pipelines with working pressure ≤1.0MPa and working temperature ≤150 ° C. The sealing material is high strength and high temperature resistant plastic binding tape. The operating principle is: use high strength high temperature resistant plastic strapping tape to wrap the leak point tightly.
1.2 Steel belt binding pressure pad plugging technology
The steel belt binding pressure pad plugging technology is applicable to straight pipes, elbows, reducing pipes, flange roots, etc., and is suitable for pipelines with working pressure ≤2.0MPa and working temperature ≤180 ° C. The plugging material is special metal steel belt and high temperature resistant rubber pad. The operating principle is: press the high temperature rubber pad to the leak point, use the steel belt tensioner to pull the steel belt, and tighten the high temperature rubber pad.
1.3 Glue plugging technology of metal fixture
The glue plugging technology of metal fixture is suitable for straight pipe, bend pipe with large bending radius, and the leakage point is weld, sand hole, crack and other areas without large area thinning and corrosion. It is suitable for pipelines with working pressure ≤20MPa and working temperature ≤900℃. The operation principle is as follows: the fixture is processed according to the shape of the pipe and pipe fitting and the size of the leak point. The fixture is a cavity at the leak point, and the edge of the cavity of the fixture is consistent with the shape of the pipe or pipe fitting. Clamp the clamp tightly, use the hydraulic pump as the power source (the pressure can reach 60MPa), push the plunger push rod in the high pressure injection gun, and press the special sealant (528) into the leaking part. The grease in the sealant (528) is quickly carbonized to solidify the asbestos fibers and establish a new sealing structure, which quickly eliminates leaks on the pipeline and achieves the purpose of sealing.
1.4 Isolated fixture plugging technology
The isolation fixture plugging technology is suitable for straight pipes, large bending radius bending pipes and significantly thinning and large-scale corrosion around the leak point, if the use of glue plugging technology is easy to inject sealant (528) into the pipeline or even the risk of pipeline interruption, suitable for the working pressure ≤10MPa, working temperature ≤900℃ of the pipeline. The principle of plugging is according to the pipe, pipe shape and leakage point size processing fixture, fixture the whole section of corrosion or thinning pipe all wrapped into the cavity, add a valve drainage in the lower part of the fixture space, establish a sealing groove between the cavity of the fixture and the fixture periphery, pour glue into the sealing groove to isolate the medium and the fixture outside, and finally turn off the drainage valve to achieve the plugging effect.
The comparison of four pipeline leakage plugging methods: binding method and steel strip method are only suitable for low pressure, low temperature and single point leakage. Fixture gluing method can be used at all temperatures and pressures, and has a wide range of use, its disadvantage is that it is not applicable when the leakage point corrosion is serious, multi-point leakage, and pipeline thinning. The isolated fixture plugging technology is a new technology, a supplement to the fixture plugging method, and a treatment method for pipeline multi-point leakage, corrosion thinning and other serious conditions. This kind of isolation fixture plugging technology is suitable for the company’s liquid ammonia leakage, acid-base medium, combustible gas, pipeline thinning and serious corrosion pipeline. It makes up for the gap in our previous plugging, and its disadvantage is that there is enough clamping space around the leakage part and the production time of special fixture for processing.
2, pipe flange leakage with pressure plugging technology
2.1 Fixture injection plugging method
The metal fixture plugging technology is suitable for all flange leaks, regardless of size, reducing diameter, eccentricity, temperature from -200℃ to 900℃, all pressures can be used. The operating principle is: according to the dimensions of the pipe flange, the clamping fixture is installed on the leakage flange to form a cavity, and then the sealant (527) is injected into the fixture through the injection thread on the fixture, so as to establish the sealing cavity to achieve the plugging effect.
2.2 Steel tape bundling and glue plugging technology
The steel belt binding and glue plugging technology is suitable for flange gasket leakage, suitable for flange with working pressure ≤2.5MPa and working temperature ≤450℃. The material is special steel strip, high temperature resistant flexible sealant. The operation principle is: tighten the steel belt along the outer diameter of the flange; Remove the flange nut, install the glue injection nut, connect the high pressure glue injection gun, and inject glue to the flange gasket; Replace the original flange nut.
2.3 Alloy Mosaic plugging technology
The alloy embedment plugging technology is suitable for the place where the base material around the hole is hard, and it is suitable for the flange with working pressure ≤1.0MPa and working temperature ≤180℃. The operation principle is: insert the alloy material with a certain taper into the two flanges with a hammer, then remove the flange nut, install the glue injection nut, connect the high pressure glue injection gun, and inject glue to the flange gasket.
2.4 Steel rope bundling glue plugging technology
The steel rope binding glue plugging technology is suitable for flanges with gaps greater than 5 mm, working pressure ≤12MPa, and working temperature ≤600℃. The operation principle is: use special tools to tighten the flange gap with steel rope, and then install the injection valve on the steel rope to inject sealant (527) into the leakage flange, so as to establish a sealed cavity to achieve the plugging effect.
Compared with four kinds of pipe flange leakage plugging methods, the fixture gluing method is simple, convenient and wide in use. Its disadvantage is that it requires machine tool processing, takes a long time, and can not deal with the leak point at the first time. The other three kinds of plugging methods do not need to process fixtures, convenient, fast, timeliness, but have certain limitations. (2023-11-16)